Unraveling the Secrets: The Art and Science of Non Destructive Testing Methods and Applications
- April 28, 2023
- Posted by: Vidal International
- Category: Non-Destructive Testing
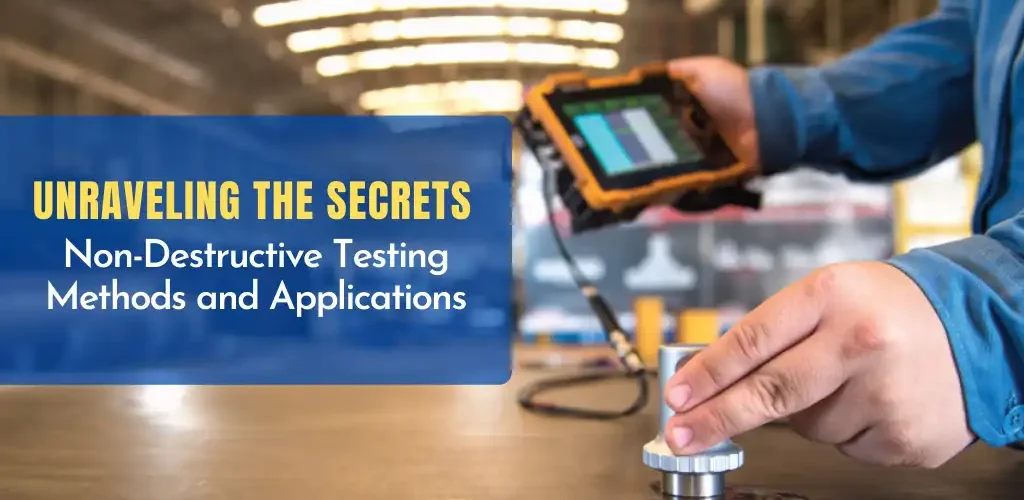
Introduction: Non-Destructive Testing – A Vital Inspection Approach
In engineering, quality control, and maintenance, non-destructive testing (NDT) is a critical inspection technique that ensures the integrity and reliability of materials, components, and structures. NDT plays a crucial role in detecting flaws, assessing the condition of assets, and preventing catastrophic failures without damaging or altering the object being examined. This article will delve deep into various non-destructive testing methods and applications, unravelling the secrets behind their effectiveness and versatility.
The Science of Non-Destructive Testing Methods
Ultrasonic Testing: A High-Frequency Solution for Flaw Detection
Ultrasonic testing, a popular non-destructive testing method, utilizes high-frequency sound waves to detect flaws and measure material thickness in various industrial applications. This technique offers several advantages, such as precise flaw detection, minimal surface preparation, and the ability to inspect complex geometries. As a result, ultrasonic testing is commonly employed in aerospace, automotive, and petrochemical industries, where the integrity of components is vital for safety and performance.
Radiographic Testing: Penetrating the Hidden Depths
Radiographic testing, another non-destructive technique, involves using X-rays or gamma rays to produce a radiographic image of an object’s internal structure. This method detects internal flaws, such as cracks, voids, and inclusions in materials like metals, plastics, and ceramics. Applications of radiographic testing span various industries, including nuclear power, construction, and automotive manufacturing.
Magnetic Particle Testing: Uncovering Surface and Subsurface Flaws
Magnetic particle testing is a non-destructive testing method that relies on the principle of magnetic flux leakage to reveal surface and subsurface discontinuities in ferromagnetic materials. By applying a magnetic field to the component under inspection, this technique enables the detection of defects such as cracks, seams, and inclusions. Widely used in industries like automotive, aerospace, and power generation, magnetic particle testing is known for its speed, reliability, and ease of use.
Liquid Penetrant Testing: A Cost-Effective Approach for Surface Flaw Detection
Liquid penetrant testing is a non-destructive method that employs capillary action to detect surface-breaking defects in non-porous materials. By applying a liquid penetrant and a developer to the surface of the component, this technique reveals flaws like cracks, porosity, and leaks. Liquid penetrant testing is commonly used in aviation, automotive, and nuclear power industries due to its cost-effectiveness, simplicity, and portability.
Non-Destructive Testing Applications Across Industries
Aerospace: Ensuring Flight Safety and Reliability
In the aerospace industry, non-destructive testing methods are indispensable for maintaining the safety and performance of aircraft components. From inspecting turbine blades for fatigue cracks to evaluating the integrity of composite materials, NDT techniques like ultrasonic testing, radiographic testing, and eddy current testing play a pivotal role in ensuring the reliability of aircraft structures and systems.
Oil and Gas: Protecting Critical Infrastructure
The oil and gas industry relies heavily on non-destructive testing methods to monitor the integrity of pipelines, storage tanks, and other vital infrastructure. Techniques like ultrasonic testing, radiographic testing, and magnetic particle testing are employed to detect corrosion, erosion, and other forms of damage that could compromise the safety and functionality of these assets.
Automotive: Driving Quality and Performance
Non-destructive testing methods are essential for maintaining the quality and performance of automotive components. From inspecting engine blocks for manufacturing defects to evaluating the durability of body panels, NDT techniques such as ultrasonic testing, radiographic testing, and liquid penetrant testing contribute to developing safe and reliable vehicles. In addition, non-destructive testing methods are crucial for ensuring the proper functioning of safety-critical systems like airbags, brakes, and suspension.
Renewable Energy: Safeguarding Sustainable Power Generation
In the renewable energy sector, non-destructive testing methods ensure the structural integrity and efficiency of wind turbines, solar panels, and other energy generation equipment. Techniques like ultrasonic testing, radiographic testing, and thermographic testing are utilized to detect defects in wind turbine blades, assess the condition of solar panel materials, and monitor the performance of other renewable energy assets.
Construction and Civil Engineering: Building a Solid Foundation
The construction and civil engineering industries benefit from non-destructive testing methods in assessing the condition of concrete structures, steel reinforcement, and other critical components. Techniques like ground-penetrating radar, ultrasonic testing, and radiographic testing help identify defects, corrosion, and deterioration in bridges, buildings, and other infrastructure, thereby ensuring public safety and prolonging the service life of these assets.
The Future of Non-Destructive Testing Methods and Applications
Technological Advancements: Pushing the Boundaries of Detection and Analysis
With the rapid advancements in technology, non-destructive testing methods are continually evolving and becoming more sophisticated. In addition, innovations in areas such as robotics, artificial intelligence, and data analysis are set to revolutionize how NDT is performed, enhancing these inspection techniques’ accuracy, efficiency, and capabilities.
Integration with Industry 4.0: Paving the Way for Smart Manufacturing
As industries embrace the principles of Industry 4.0, non-destructive testing methods are increasingly being integrated into intelligent manufacturing processes. The combination of NDT with advanced sensors, data analytics, and automation will enable real-time monitoring and predictive maintenance, resulting in more efficient and cost-effective production and quality control.
Training and Certification: Preparing the Workforce for Tomorrow’s Challenges
As non-destructive testing methods and applications continue to evolve, investing in training and certification programs is crucial to equip the workforce with the necessary skills and knowledge. Organizations like the American Society for Nondestructive Testing (ASNT) and the British Institute of Non-Destructive Testing (BINDT) offer certification programs and training resources to help professionals stay up-to-date with the latest developments in the field.
Advanced Non-Destructive Testing Techniques
Phased Array Ultrasonic Testing: Enhanced Precision and Flexibility
Phased array ultrasonic testing (PAUT) is an advanced non-destructive testing method that improves conventional ultrasonic testing by utilizing multiple ultrasonic elements to generate and receive signals. By controlling each element’s timing, amplitude, and angle, PAUT allows for greater precision in flaw detection, sizing, and characterization. In addition, its versatility makes it suitable for various applications, including weld inspections, corrosion mapping, and composite material evaluation.
Eddy Current Testing: Detecting Discontinuities in Conductive Materials
Eddy current testing is a non-destructive method that utilizes electromagnetic induction to detect discontinuities in conductive materials. By inducing eddy currents in the test object and measuring the changes in the electromagnetic field, this technique can identify surface and near-surface defects such as cracks, corrosion, and material thinning. Eddy current testing is commonly employed in aerospace, automotive, and power generation industries to inspect heat exchanger tubes, aircraft components, and other conductive materials.
Time-of-Flight Diffraction: Advanced Ultrasonic Flaw Sizing
Time-of-flight diffraction (TOFD) is a non-destructive testing technique that combines ultrasonic testing with advanced signal processing to size and accurately characterize defects. By analyzing the time it takes for ultrasonic waves to diffract around a flaw, TOFD can precisely measure defect height, length, and position. This method is beneficial for weld inspection, where accurate flaw sizing is crucial for determining the structural integrity of components.
Acoustic Emission Testing: Listening to the Sounds of Structural Stress
Acoustic emission testing is a non-destructive testing method that involves monitoring the sounds emitted by materials and structures under stress. As defects, such as cracks, propagate and grow, they release energy through acoustic waves. By detecting and analyzing these acoustic emissions, this technique can identify defects’ location, severity, and growth rate. Acoustic emission testing is often used with other NDT techniques for monitoring the structural health of bridges, pressure vessels, and other critical infrastructure.
Thermographic Testing: Visualizing Temperature Differences for Flaw Detection
Thermographic testing, also known as infrared testing, is a non-destructive testing method that uses thermal imaging cameras to detect temperature differences on the surface of materials and structures. This technique can identify defects such as delamination, voids, and water ingress in composites, plastics, and concrete by visualizing the heat distribution. Thermographic testing is commonly used in building inspections, aerospace applications, and maintenance of electrical systems.
Non-Destructive Testing Standards and Regulations
The Role of Standards and Regulations in NDT
Non-destructive testing methods and applications are subject to numerous international, national, and industry-specific standards and regulations. These guidelines ensure the quality, consistency, and reliability of NDT practices and the competency of NDT personnel. Adherence to standards and regulations is crucial for maintaining the safety and performance of materials, components, and structures across various industries.
Key Non-Destructive Testing Standards Organizations
Several organizations are responsible for the development and maintenance of non-destructive testing standards, including:
- American Society for Testing and Materials (ASTM): ASTM publishes various NDT standards covering methods like ultrasonic testing, radiographic testing, and magnetic particle testing. International Organization for Standardization (ISO): ISO develops and maintains international NDT standards, such as those related to eddy current testing, ultrasonic testing, and liquid penetrant testing.
- American Society of Mechanical Engineers (ASME): ASME is responsible for creating and maintaining NDT standards for various industries, including pressure vessel and piping inspection, nuclear component fabrication, and construction.
- American Petroleum Institute (API): API develops standards and recommended practices for the oil and gas industry, addressing non-destructive testing methods such as radiographic testing, ultrasonic testing, and magnetic particle testing.
Importance of Compliance with Non-Destructive Testing Standards
Compliance with non-destructive testing standards is essential for several reasons:
- Safety: Adherence to NDT standards ensures that inspection methods are performed correctly, minimizing the risk of undetected flaws and catastrophic failures.
- Quality Control: NDT standards provide guidelines for the practical application of inspection techniques, ensuring the accuracy and reliability of test results.
- Regulatory Compliance: Many industries are subject to regulatory requirements that mandate using specific NDT methods, personnel qualifications, and procedures. Compliance with these standards is necessary to avoid fines, penalties, and potential shutdowns.
- Market Competitiveness: Companies that adhere to NDT standards demonstrate their commitment to safety and quality, which can lead to increased business opportunities and a competitive edge in the marketplace.
Challenges and Solutions in Non-Destructive Testing
Overcoming Inspection Limitations
While non-destructive testing methods offer numerous advantages, they also have inherent limitations. For example, some techniques may not be suitable for specific materials or geometries, while others may be sensitive to environmental factors like temperature and humidity. To overcome these limitations, NDT practitioners must stay up-to-date with the latest technological advancements and best practices in the field and employ a combination of complementary inspection methods when necessary.
Ensuring the Competency of NDT Personnel
The effectiveness of non-destructive testing methods relies heavily on the skills and competency of NDT personnel. To ensure accurate and reliable test results, companies must invest in comprehensive training and certification programs covering theoretical knowledge and practical skills. In addition, promoting a culture of continuous learning and professional development can help NDT practitioners stay current with industry trends and emerging technologies.
Managing and Analyzing Large Volumes of Inspection Data
As non-destructive testing methods become more advanced and automated, they generate increasingly large volumes of inspection data. Effectively managing and analyzing this data is critical for optimizing inspection processes, detecting trends, and making informed maintenance decisions. Companies can leverage advanced data analytics, machine learning algorithms, and data visualization tools to address this challenge to gain actionable insights from their NDT data.
Adapting to Industry-Specific Requirements and Regulations
Non-destructive testing methods and applications must be tailored to various industries’ specific requirements and regulations. This can involve developing specialized inspection techniques, adapting existing methods to new materials and geometries, and compliance with industry-specific NDT standards. To stay competitive and relevant, NDT practitioners must be knowledgeable about their target industries’ unique challenges and demands and be prepared to adapt their inspection methods accordingly.
Conclusion: The Ongoing Evolution of Non-Destructive Testing
Non-destructive testing methods and applications continue to evolve and expand, driven by technological advancements, industry demands, and regulatory requirements. As companies strive to maintain the safety, performance, and reliability of their materials, components, and structures, NDT practitioners must stay informed and adaptive, embracing new technologies and best practices to overcome challenges and deliver accurate, reliable inspection results.
To get the best NDT course training check below: